Information Library
Determining the maximum cable length when using the remote sensor function with A&D’s weighing indicators
To determine the maximum cable length, the following values are necessary: the cross-sectional area of cable conductor, the electrical resistance between input terminals of the load cell, and the number of load cells. When using A&D’s weighing indicators, the allowable two-way resistance for cables is about 10% of the resistance between the input terminals of the load cell. Therefore, the one-way resistance is about 5%. The resistance of copper wires with a cross sectional area of 1 mm2 is calculated as 0.02 Ω/m. The formula when using one load cell is as follows: The maximum cable length = the allowable cable resistance ÷ the cable resistance per meter. When two or more load cells are used, the formula is as follows: The maximum cable length = the allowable cable resistance ÷ the cable resistance per meter ÷ the number of load cells.
As an example, let’s calculate the maximum cable length when using three A&D LCC11 load cells with KO162 load cell cables.
The resistance between the input terminals of the LCC11 is 800 Ω.
The allowable cable resistance is 5%. KO162 load cell cables have a cross-sectional area of 0.5 mm2 so the resistance is 0.04 Ω/m.
The maximum cable length = 800 x 0.05 ÷ 0.04 ÷ 3
In this case, the maximum cable length is 333 m.
While the calculated length is 333 m, it may not be possible to use a 333 m cable in some environments (such as areas with a large amount of noise).
The following charts show the relation between the thickness and allowable length of load cell cables.
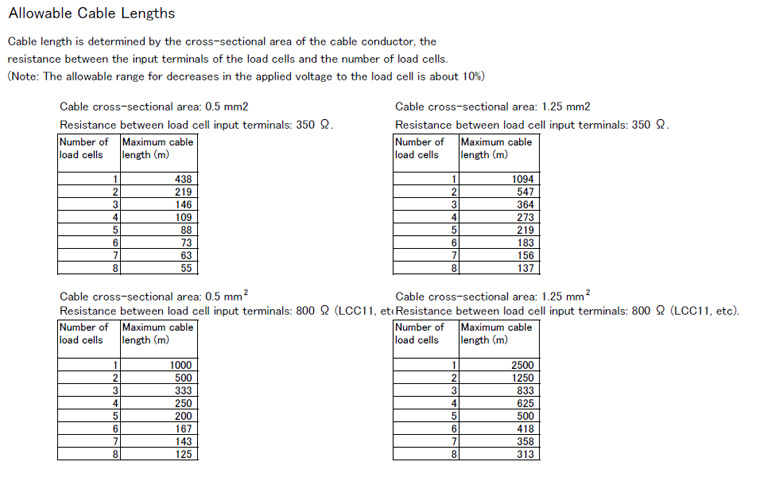